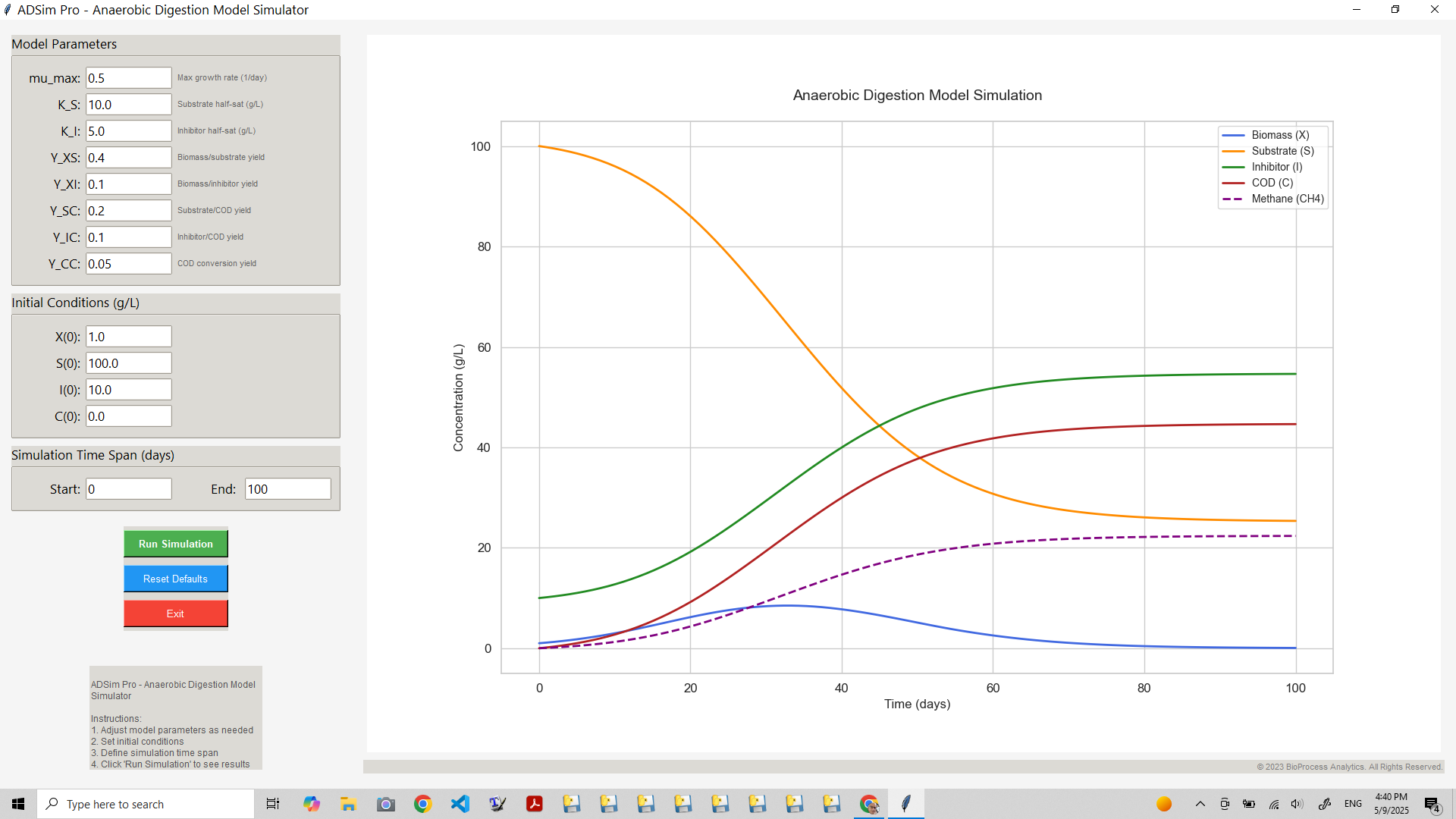
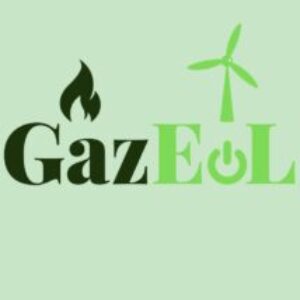
Hatem
Forum Replies Created
Thank you for sharing your perspective. I respectfully disagree with your assessment, as it underestimates both the current capabilities and the future potential of AI tools in anaerobic digestion (AD) operations. Your comments reflect a conventional, lab-centered view of process management, which does not scale effectively to the operational complexities of commercial facilities.
First, scaling up from lab tools and Excel-based forecasting to full-scale plant operations is not a linear process—they are fundamentally different worlds. A commercial digester processing tons of heterogeneous feedstock per day, with fluctuating input composition, operational disturbances, and dynamic energy markets, demands a level of system-wide integration and predictive capacity that simply cannot be met with spreadsheets and manual inputs alone. What works in a stable academic or pilot setting does not generalize to the volatile conditions of real-world operations.
Second, the AD business does not operate like traditional chemical processing plants where one-size-fits-all lab routines suffice. We’re dealing with living systems that vary daily in microbial dynamics, temperature responses, substrate synergy, and inhibition potential. AI excels at learning patterns in such complex, non-linear systems—especially when combined with continuous or semi-continuous data acquisition.
Regarding your valid point that AI needs data from conventional tests—yes, absolutely. But the value of AI is in how it connects, interprets, and predicts using these data streams. It doesn’t replace chemistry or expertise—it augments them.
On the concern that plant owners might not want to share their data for training purposes: that is a business model and data governance issue, not a limitation of the technology. Models can be customized per facility and trained solely on their own data to protect IP while still yielding substantial insights. AI is not just for optimizing yield; it’s about risk mitigation, early fault detection, and predictive maintenance—key to uptime and revenue protection.
Also, the argument about sensing technologies not being perfect is fair but misses the point: AI doesn’t depend on a single sensor. Its strength is in integrating multiple imperfect signals to yield a robust forecast or recommendation. It’s the same principle we trust in aviation, finance, and weather forecasting.
Finally, and critically:
1. Building a structured, historical data repository is essential for consistent operational knowledge transfer. This ensures that insight doesn’t walk out the door when a staff member leaves. AI or not, data discipline adds resilience to your operation.
2. A historical database supports standardization and benchmarking. With structured records, operators can compare performance across years, seasons, or feedstock shifts, and refine their strategy accordingly. It’s not only about AI; it’s about professionalizing operations and making informed decisions with traceability.
In short, AI tools are not a silver bullet, but to dismiss them based on lab-scale practices and assumptions about operator skill levels is to ignore the operational reality and business potential of modern digesters. We’re not replacing people—we’re giving them better tools to compete in a changing energy and waste landscape.
Would be glad to continue the conversation and share some concrete examples where data-driven models have made a measurable difference in well-performing plants.
Note:
I’ve attached a quick example from one of our applications, LimusAI, that shows how AI can precisely identify which features have the greatest impact on biogas production at a given site. This level of insight empowers operators with targeted, data-backed decisions that go far beyond what’s possible with manual tools alone.Hatem
Member29 May 2025 at 11:50 am in reply to: Why don’t more biogas & RNG plants capture and use CO2?I see opportunity in CO2 from AD :
Capturing CO₂ from biogas and using it to grow algae.
This offers a powerful, climate-friendly synergy: algae thrive on CO₂, and biogas upgrading produces a steady stream of biogenic CO₂ that would otherwise be wasted. This creates a circular system where CO₂ and nutrient-rich digestate from anaerobic digestion fuel algae growth, which can in turn produce high-value products like biofuels, bioplastics, or animal feed. Despite the scientific potential, practical barriers such as gas purification needs, mismatched CO₂ supply and light availability, land and water requirements, and immature markets have slowed adoption. However, with advances in algal biotechnology, modular reactor systems, and stronger policy support for CO₂ reuse and nutrient recycling, integrating algae cultivation with RNG plants could become a game-changer for both carbon capture and the bioeconomy.
While this advice is sound in principle, it’s important to acknowledge that, in a real-world operational context, manually controlling all the variables influencing digester performance is extremely complex—if not impossible. This is where AI becomes essential. By analyzing large volumes of operational data, AI can help identify the key parameters that require attention and guide operators on what to adjust, and when, to maintain optimal conditions.
I recommend tracking the amount of digestible energy fed to the digester daily and comparing it to the biogas output. If gas production doesn’t align with the expected energy input, it may indicate a need to investigate potential inhibition.
ThanksHatem
Member28 May 2025 at 10:52 am in reply to: Microbiology and artificial intelligence in the industryPassive monitoring or active parametrisation?
We often use sensitivity analysis to understand how key input variables—like feedstock variability or temperature shifts—impact model outputs and system performance. We’ve built tools and methods, such as the Sobol method, to help identify the most influential parameters in different operational scenarios.
Thanks!
Hatem
Member28 May 2025 at 10:07 am in reply to: Microbiology and artificial intelligence in the industryThank you Natalia for the excellent question.
I think that Microbiology and Artificial Intelligence (AI) can work synergistically to optimize and revolutionize anaerobic digestion (AD) processes in several impactful ways. However, leveraging AI effectively requires a deep understanding of the microbiological and kinetic aspects of the system:
1- Deep Understanding of AD Compartment Interactions
An AI engineer must first gain a solid grasp of the biological and chemical interactions between the compartments of the AD process — hydrolysis, acidogenesis, acetogenesis, and methanogenesis. Each phase involves distinct microbial communities and specific metabolic pathways. AI models built without this understanding risk oversimplification, which can lead to misleading predictions or poor control strategies.
2- Awareness of Kinetic Dynamics Across Phases
Each phase of AD operates at different kinetic rates. For instance, hydrolysis (especially of complex lignocellulosic substrates) is often the slowest step, while acidogenesis can proceed relatively quickly once soluble compounds are available. Recognizing these differences helps AI systems account for temporal lags and bottlenecks in biogas production, enhancing both prediction and control algorithms.
3- Experimental Validation with Substrate Characteristics
Before building robust AI models, it is essential to conduct lab-scale experiments (or have historical data) to understand how varying substrate characteristics — such as C/N ratio, particle size, or biodegradability — affect microbial activity and gas yield. These empirical insights feed valuable input data to train and validate AI models.
4- Microbial Growth Rate Modeling
Effective AI systems should integrate established microbiological kinetics, such as Monod, Haldane, or Contois models. These equations differ in how they represent substrate inhibition or nutrient limitation, and their selection affects the accuracy of growth rate predictions under dynamic loading conditions.
5- AI-Driven Optimization and Control
Once trained with high-quality biological, kinetic, and operational data, AI algorithms — such as machine learning or reinforcement learning models — can be deployed to:
— Optimize feedstock mixtures for maximum biogas yield
— Predict system failures or process upsets before they occur
— Provide real-time operational recommendations (e.g., adjusting organic loading rates)
— Reduce downtime and improve reactor stability through adaptive control
Thanks you
That’s a great question Ryan—and one I’ve been reflecting on as well.
With the growing availability of small and micro-scale upgrading technologies, combined with innovations like RNG-powered farm equipment, I believe RNG is becoming increasingly feasible in remote areas. These advancements lower the barriers to entry for decentralized energy production, which is particularly important where traditional infrastructure is limited or costly to extend.In fact, I’ve had the opportunity to work on several projects in remote regions where being energy autonomous wasn’t just a preference—it was a necessity for the residents. In those settings, RNG played a key role in supporting local resilience. It allowed communities to make use of on-site organic waste, reduce their reliance on diesel or other fossil fuels, and stabilize their energy supply in a more sustainable way.
While CHP systems certainly have their advantages, especially in larger, centralized installations, RNG offers a flexible and scalable alternative. It’s especially promising for farms and smaller communities looking to close local loops and align with environmental goals. As the technology matures and the economics continue to improve, I do see RNG becoming not just a viable option, but a compelling one in many remote and rural contexts.
Thanks 🙂From my professional perspective, the cost of biogas upgrading for a plant producing poor-quality biogas—characterized by high levels of impurities such as 6,000 ppm H2S, elevated moisture, or siloxanes—can be substantial, driven by the need for robust pretreatment and upgrading systems to meet stringent biomethane standards. Capital expenditure (CAPEX) encompasses equipment like biological or chemical H2S scrubbers, CO2 removal units (e.g., membrane separation or amine scrubbing), dehumidifiers, and siloxane filters, with costs for a 1,000 Nm³/h plant ranging from $500,000 to $2 million, often leaning toward $1–1.5 million for low-quality biogas due to larger, more complex systems, plus 20–30% for installation, engineering, and permitting. Operating expenditure (OPEX) includes frequent replacement of consumables (e.g., activated carbon at $2–$5/kg or caustic chemicals at $0.5–$1/kg), energy for pumps and aeration, maintenance, and hazardous waste disposal, totaling $50,000–$200,000/year, with high H2S potentially driving costs toward $100,000 annually for chemicals ($40,000), energy ($30,000), maintenance ($20,000), and waste handling ($10,000). These elevated costs, compared to $300,000–$500,000 CAPEX and $20,000–$50,000/year OPEX for cleaner biogas, underscore the importance of tailoring system design to biogas quality to optimize long-term economics.
To sidestep the costly challenges of upgrading poor-quality biogas with high H2S (e.g., 6,000 ppm), moisture, or siloxanes, I advocate a strategic approach that leverages AI modeling alongside proactive process optimization for a cleaner, more cost-effective operation. From my perspective, integrating AI-driven predictive models can transform biogas pretreatment by forecasting impurity levels based on feedstock composition, digester conditions, and operational data, enabling preemptive adjustments. For instance, AI can analyze historical and real-time data (e.g., pH, temperature, sulfur content) to optimize anaerobic digestion, minimizing H2S production at the source by recommending ideal feedstock blends or process parameters—say, avoiding sulfur-rich inputs like manure or protein-heavy food waste.Hatem
Member27 May 2025 at 1:08 pm in reply to: Biogas pretreatment – what is the cost for projects?From my point of view, choosing the right biogas pretreatment is a balancing act that hinges on understanding both upfront and ongoing costs, and I’ve seen how getting this right can make or break a project’s success. Capital expenditure (CAPEX) covers the initial investment—think reactors, scrubbers, media beds like activated carbon or iron oxide, plus pumps, piping, and instrumentation, along with site prep, engineering, and integration into existing systems. You’ll also need gas analyzers and control systems for monitoring, not to mention permitting and design to meet regulations, which can add up fast. On the operating expenditure (OPEX) side, you’re looking at ongoing costs like replacing consumables—activated carbon, iron oxide, or caustic chemicals like NaOH for scrubbing—plus electricity for pumps, blowers, or heating, especially for biological systems in colder climates. Maintenance, including labor and spare parts, is another factor, as is disposing of spent media or liquid waste, which can get pricey if it’s classified as hazardous. Regular H2S and gas quality testing is a must to keep things compliant, and I think nailing down these costs early, tailored to your specific H2S levels and flow rates, is key to picking a system that’s both effective and economical.
Industry trends suggest that for high H2S levels (e.g., 6,000 ppm), operators often prefer biological or liquid redox systems for their efficiency and lower long-term costs, especially in large-scale plants. For smaller facilities or lower H2S levels (e.g., 100 ppm), activated carbon or iron oxide systems are more common due to their simplicity and lower upfront costs.
I believe that early actions play a crucial role in either building or damaging community trust. I advocate for a balanced approach that combines effective communication with strong technical performance, as this is vital for the success and sustainability of projects.
I think that Artificial Intelligence (AI) holds transformative potential for advancing anaerobic digestion by pinpointing the optimal mix of process variables to maximize biogas production. But, its true power lies not in generic modeling but in capturing the unique biochemical dynamics of each plant. Anaerobic digestion is more than a statistical system—it’s a living, adaptive process driven by complex interactions among substrates, microbial communities, and operational parameters. As such, models must be meticulously crafted, grounded in a deep understanding of biochemical mechanisms and powered by high-quality, plant-specific historical data.
At GazEoL, we recognize and embrace the inherent complexities of anaerobic digestion, which has guided the development of a dynamic AI framework that thoughtfully combines advanced machine learning with deep scientific insight.
Informed by our contributions to peer-reviewed research, our approach enables us to generate nuanced, reliable predictions—carefully adapted to the specific conditions and character of each biogas facility.At GazEoL, we support our clients in this process by applying AI and advanced numerical modelling. This allows us to simulate plant behavior, identify optimal operating conditions, and detect early signs of instability with greater accuracy and confidence.
Thanks again for your question!
Good Question Natalia.
Specifically, determining whether the Organic Loading Rate (OLR) is optimal best :
During the design stage of the biogas plant—closely linked with the Biochemical Methane Potential (BMP) test—as well as during start-up, after changes in feedstock, before scaling up, following operational interruptions, or when signs of instability appear (e.g., pH drop, VFA rise, reduced gas yield).
Regular monitoring of key indicators like biogas production, pH, alkalinity, VFA levels, and methane yield is essential.
Gradually increasing the OLR while observing for stress signals helps identify the optimal point where efficiency is maximized without compromising microbial stability.
Thanks for your question
Hatem
Member1 June 2025 at 8:13 am in reply to: Daily operations at biogas and RNG plant – what is important to watch and howHi Adarsha.
I answer your question with great pleasure.
For anaerobic conditions, we typically refer to COD (Chemical Oxygen Demand) or biogas potential (e.g., BMP tests—Biochemical Methane Potential), since oxygen is not involved in anaerobic degradation.
However, BOD is particularly valuable for identifying the readily biodegradable fraction, optimizing feedstock mix, and ensuring stable and efficient biogas production—especially in agriculture or MSW-based plants dealing with variable, organic-rich inputs.
Cheers
Hatem
Member26 May 2025 at 10:54 am in reply to: Financial viability of biogas and RNG (biomethane projects)Very True Nikan,
In several energy cost analysis reports, it is noted that Quebec has fewer opportunities to generate low-cost CC1 credits, primarily due to its limited local oil and fuel production. Since many CC1 credits come from reducing emissions in fuel production and refining, and Quebec relies mostly on imported fuels, these options are limited. Also, Quebec’s clean energy system means there are fewer large fossil fuel projects to improve. As a result, Quebec tends to depend more on credits from cleaner fuels and advanced vehicle technologies, which are generally higher in cost.
Note:
Since Quebec has limited local oil production (fewer CC1 opportunities), it relies more on these CC2 and CC3 credits. However, these tend to be more expensive to produce or procure, which means overall compliance costs can be higher for Quebec compared to provinces with more CC1 credit opportunities.